The VSR - Lastest generation
Useful format
Many machines equipped with several modules impose constraints inherent to the physical offsets between the tools. Indeed, it is not always possible to work everywhere on the table with all the tools, and this complicates the use and limits the possibilities.
On the VSR, milling cutters, blades, scoring wheels, taps, 3D sensor, camera, LASER pointer, etc. all work in the full format of the machine, without delay.
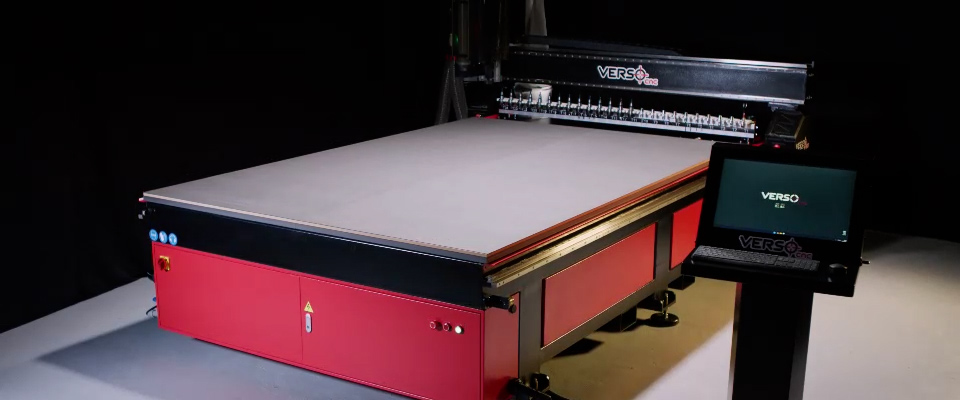
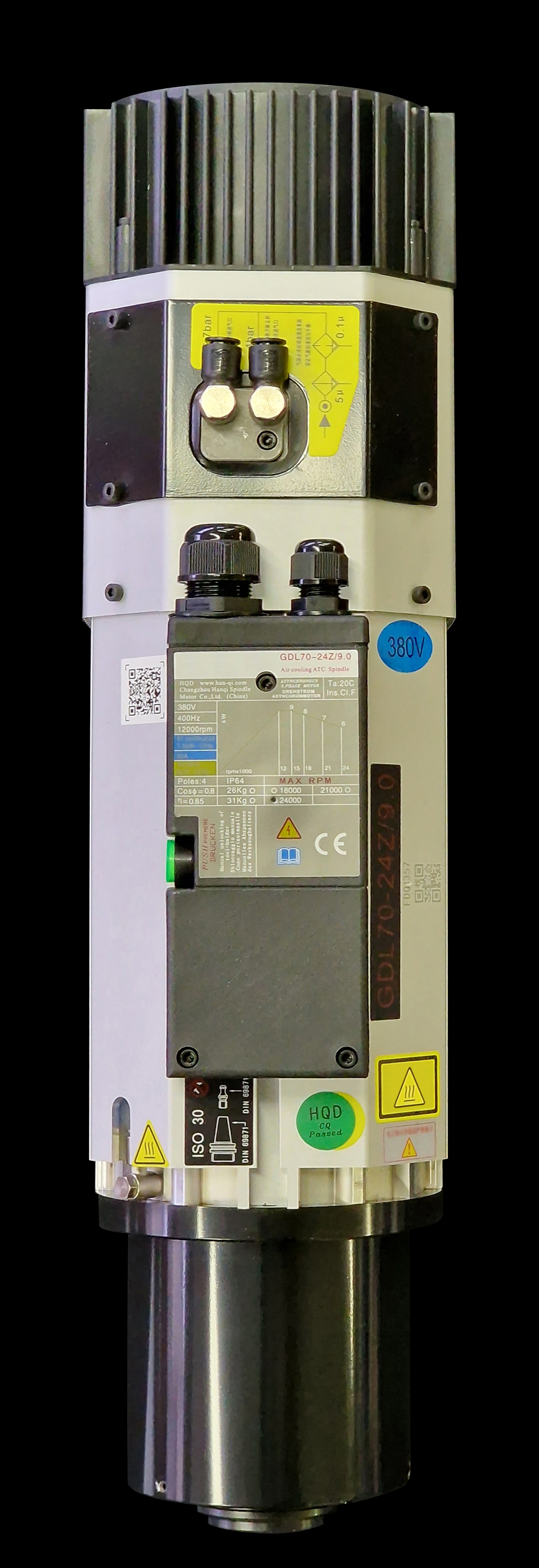
Why a 9 KW spindle ?
Again, this is a matter of versatility...
When machining with small-diameter tools, it is necessary to work with a relatively high rotational speed. Too low a speed would impose slow cuts. The required torque is quite low. A quick but not very powerful spindle may be suitable in this case.
Conversely, work requiring large-diameter tools (large milling cutters, countersink cutters, shaped milling cutters, wood cutters, etc.) requires a much lower speed but a much greater torque. Some low-power spindles can deliver the necessary torque at low speed and thus carry out this work.
But these are different types of spindles! The only way to combine these capacities on the same spindle is for it to be able, on demand, to reach a high speed and/or a high torque. The max power is the multiplication of these two values, which is why it may seem high.
The spindle of the VS is therefore able to optimally carry out completely different work by only rarely using high power.
Motorisation
The brushless AC servomotors fitted to our machines are very widely sized to fully meet the requirements of milling work (strength and rigidity) but also tangential cutter work (high speed and high accelerations).
The permanent position control via 26-bit encoders ensures perfect precision.
Depending on the tool used, the actual work speed reaches 57 mm/min.

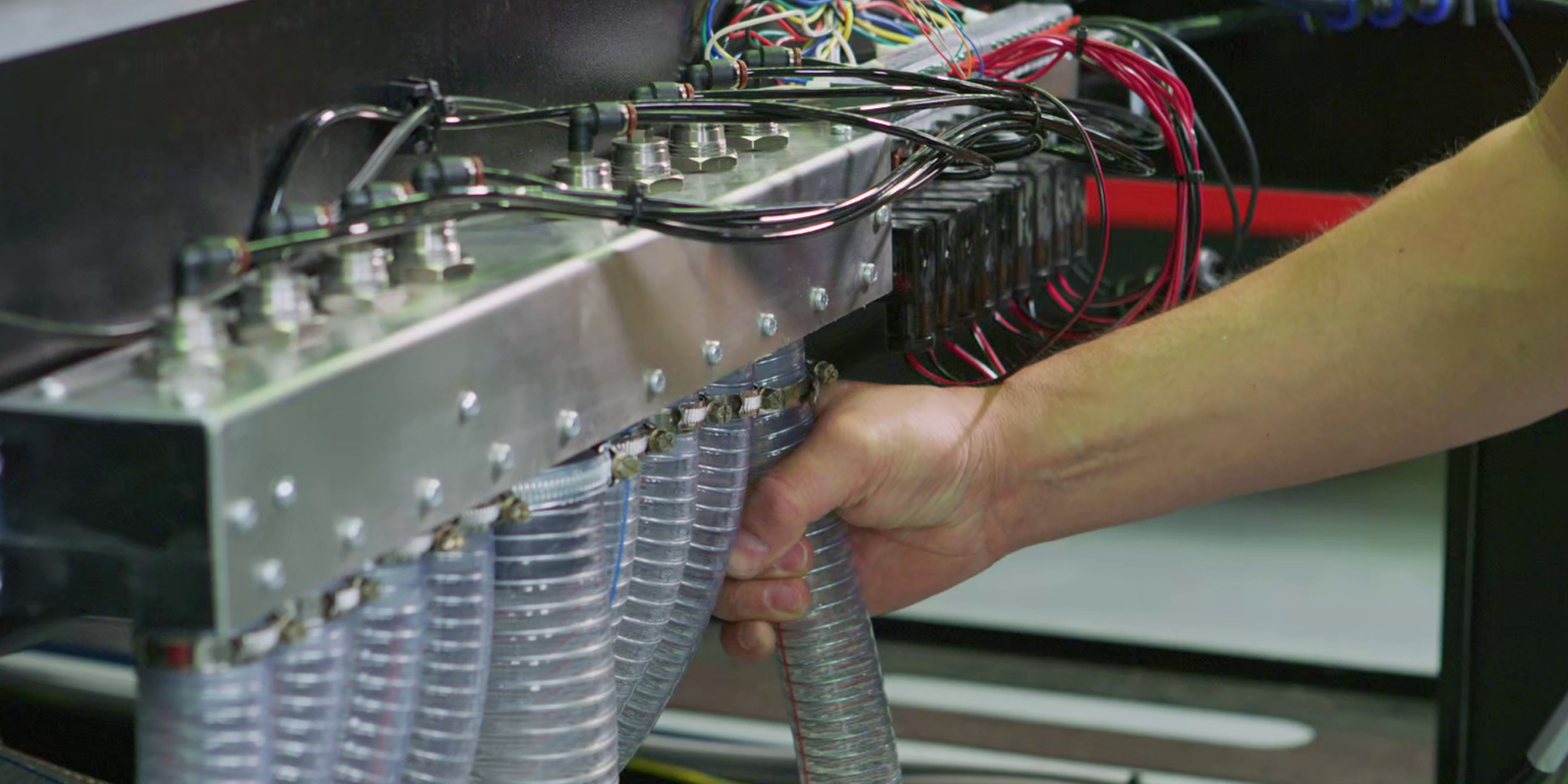
Vacuum tracking
The VSR is equipped with a multi-zone vacuum table (12 zones on a VS2030R).
This is put under vacuum by a double-stage turbine. In order to maximise the performance of holding the parts during cutting, the opening/closing of each zone is dynamically controlled by the software during cutting. This management also makes it possible to limit the power consumption of the vacuum table.
"Smart Power"
In parallel with the management of the zones, the vacuum is continuously analysed by a sensor and the software modulates the power delivered by the turbine according to the need.
As an example, this makes it possible to cut letters in Dibond® 35 cm high by mobilising only a suction power of 800 W!
On this type of work and given the current cost of energy, the savings compared to a conventional milling machine can exceed 400 euros per month!
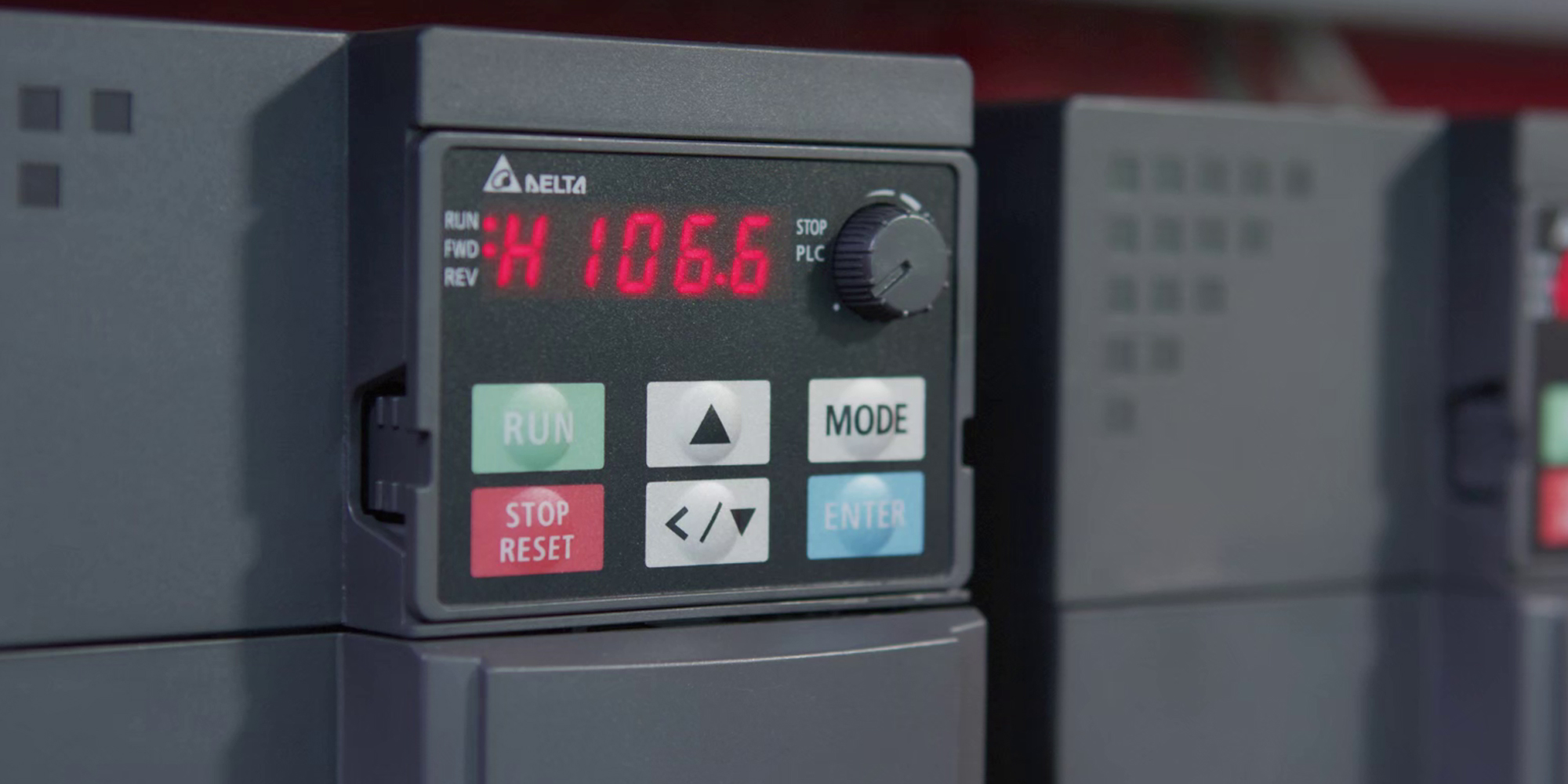
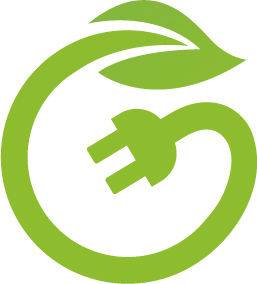
But for parts that are difficult to maintain at the end of cutting (small parts, very fine materials), the software can itself engage a high power (up to 10 KW), but only on the last millimetres of cutting.
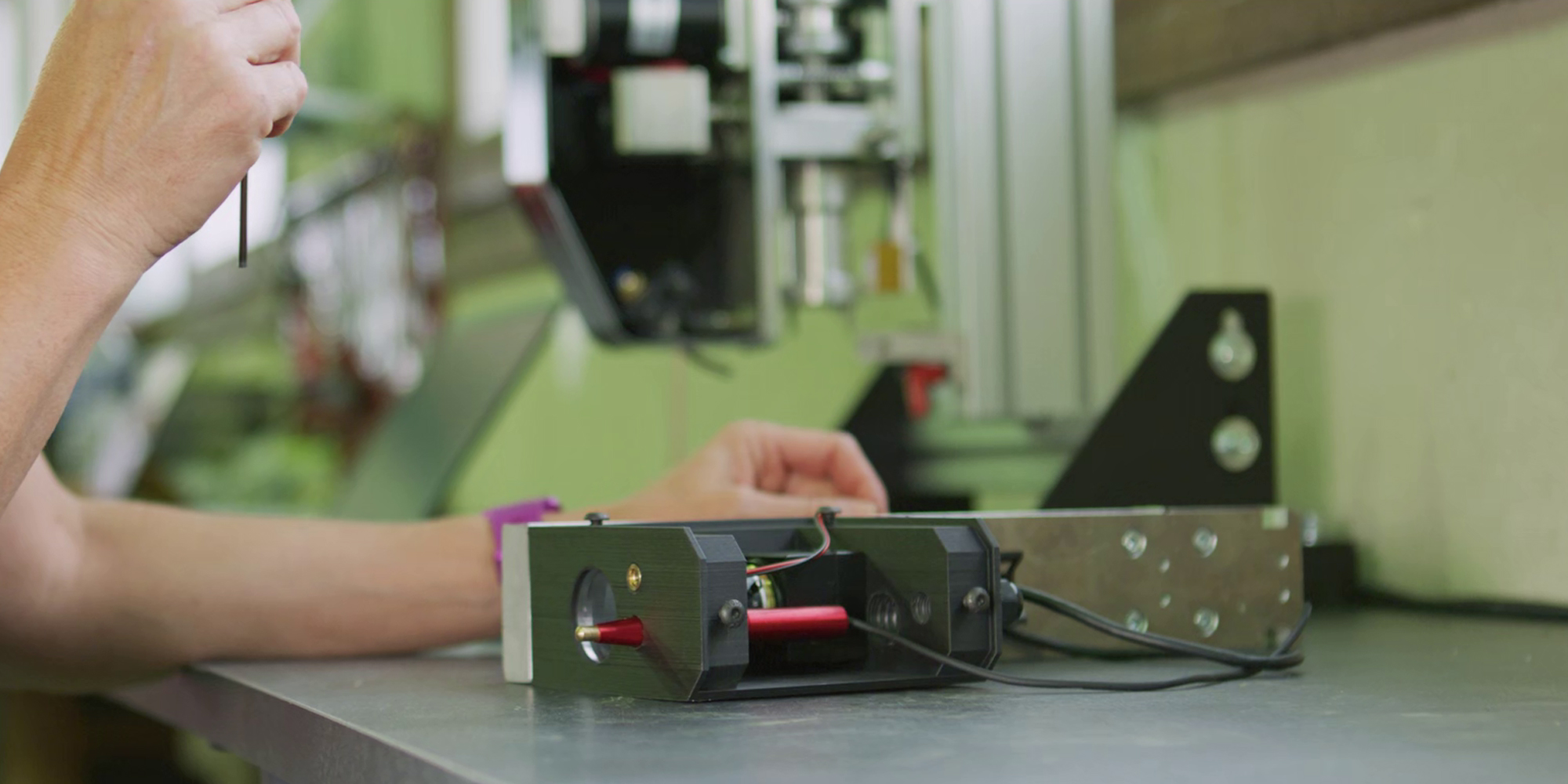
Camera
Printing – double-sided cutting
On the front side, the machine scans the printed marks as well as the corners of the plate. If necessary, cuts or engravings are made.
After the operator turns the plate over, the plate corners are scanned and the reverse work starts.
N.B.: It is possible to use the plate angle scan to carry out simple double-sided work (without printing). This function can also be used to precisely position a cutting in a plate.
These functions are almost essential for the creation of "hinges" in Hylite, the alignment between the machined faces must be perfect.
The VERSO CNC driver is available from Caldera®
VERSO CAM includes 2 Illustrator plugins to add the marks and create the cutting files.
Sensing of materials
Some materials have a thickness that varies greatly from one place to another on the same plate. This is, for example, the case of the cast PMMA, where there is a gap of up to 1 mm between the edges and the middle of the plate. A 1 mm deep engraving could "pass over" the material in places and burrow more than a millimetre at others...
In VERSO CAM, when we request a cutting in a material concerned by these variations and that the cutting contains non-through work (grooves, engravings, pockets, etc.), at the time of launching the work, the software offers a prior sensing of the material. If the operator validates this step, the 3D sensor then takes an accurate reading of the plate, then the (corrected) machining will be launched automatically, in the process.
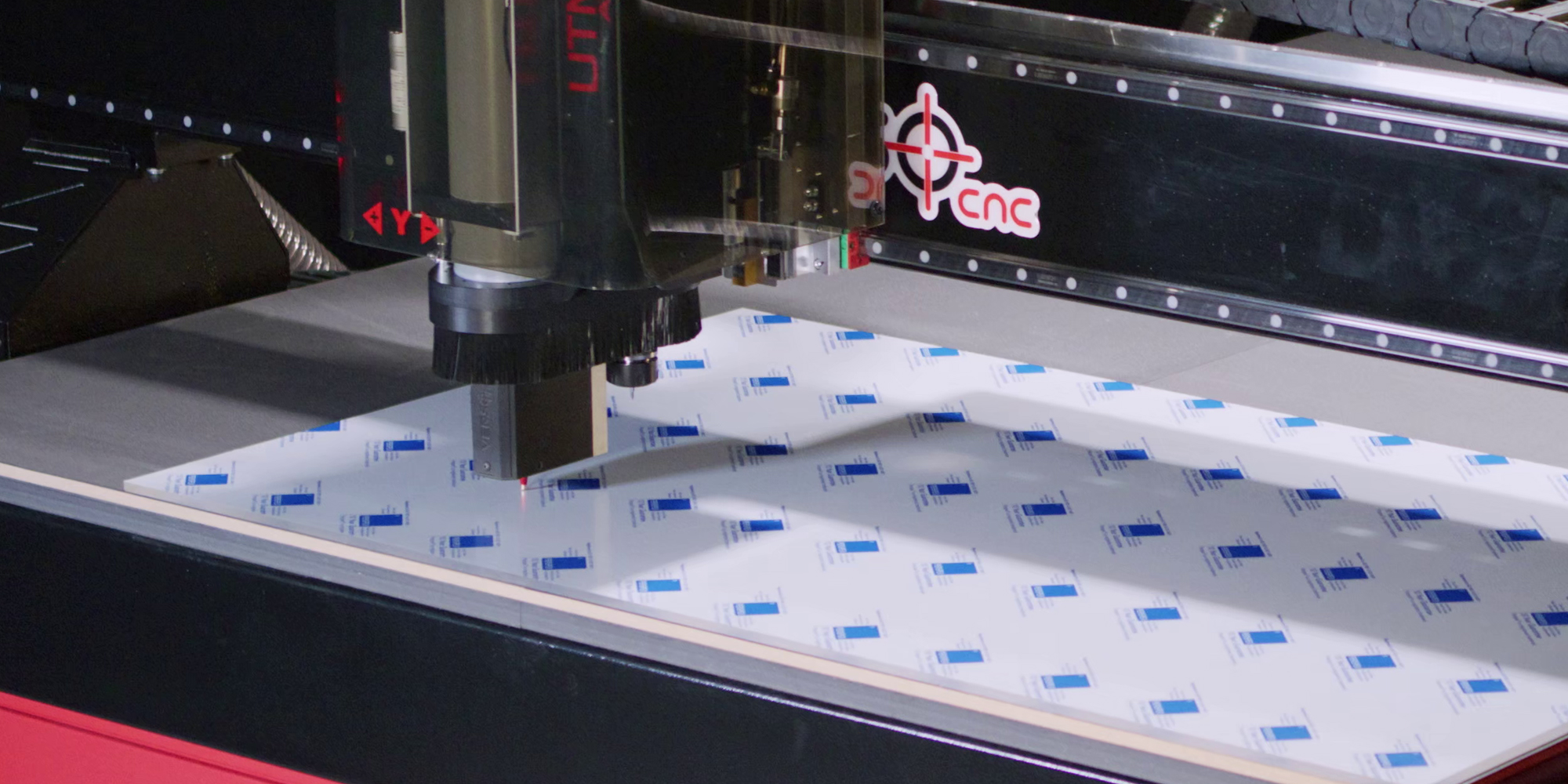
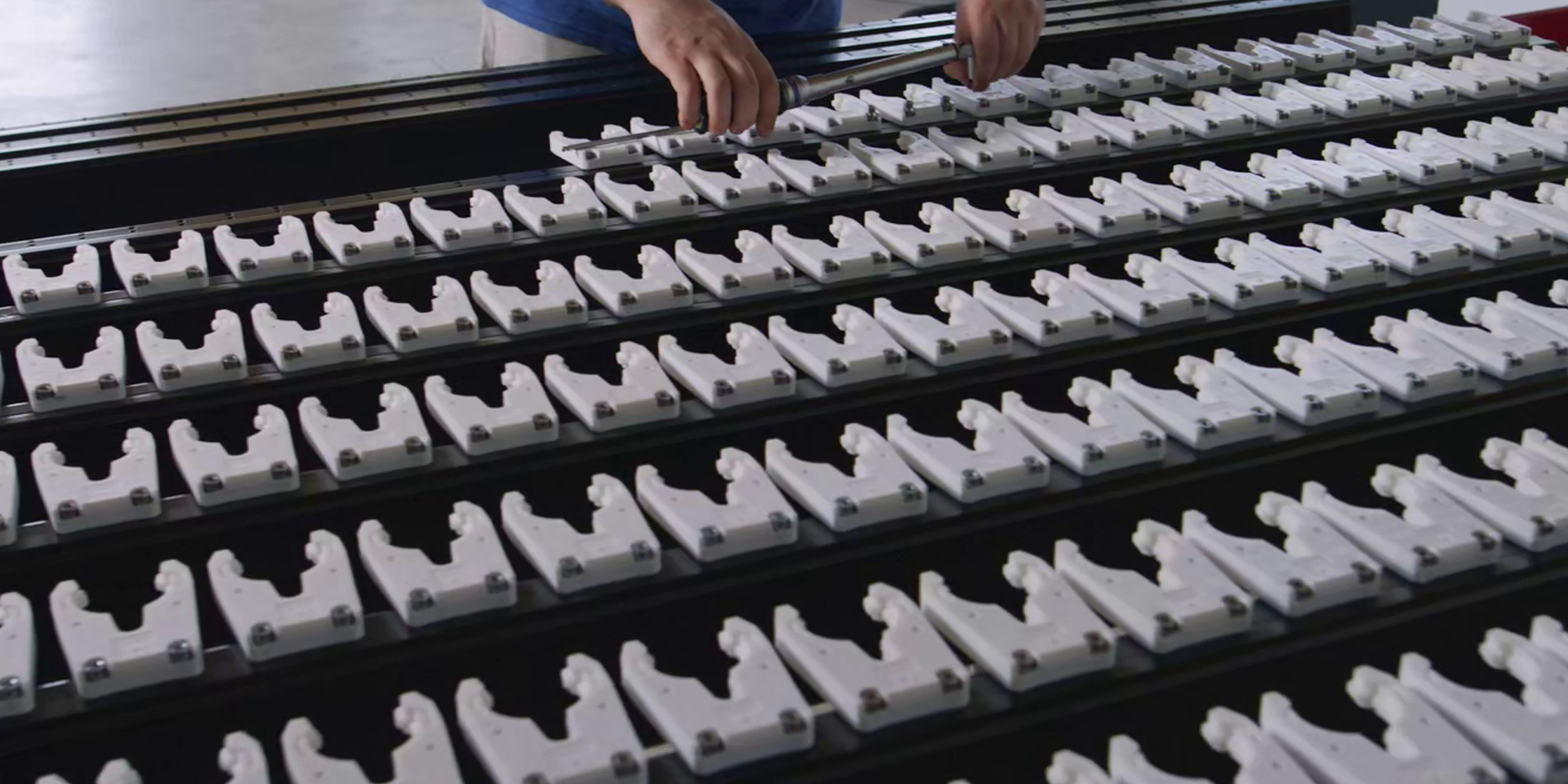
The tool magazine
Placed at the bottom of the VSR, the 24-tool magazine supports the ISO 30 cones for milling cutters and drills. It also hosts the VERSO UTM tools (tangential blades, oscillating blades, V-cutters, scoring wheels and taps).
Many sensors secure the various steps and protect the machine as much as possible from possible operator errors.
The automatic tool sensor
Ultra precise, the electronic gauge sensor is automatically used by the control software. In addition to guaranteeing the accuracy of the working depths, it makes it possible to detect a possible tool breakage.
It is automatically cleaned by a jet of compressed air a few moments before the measurement so that it cannot be distorted by dust or chips. All tools (milling cutters, blades, V-cutters, taps and scoring wheels) are measured by the tool sensor.
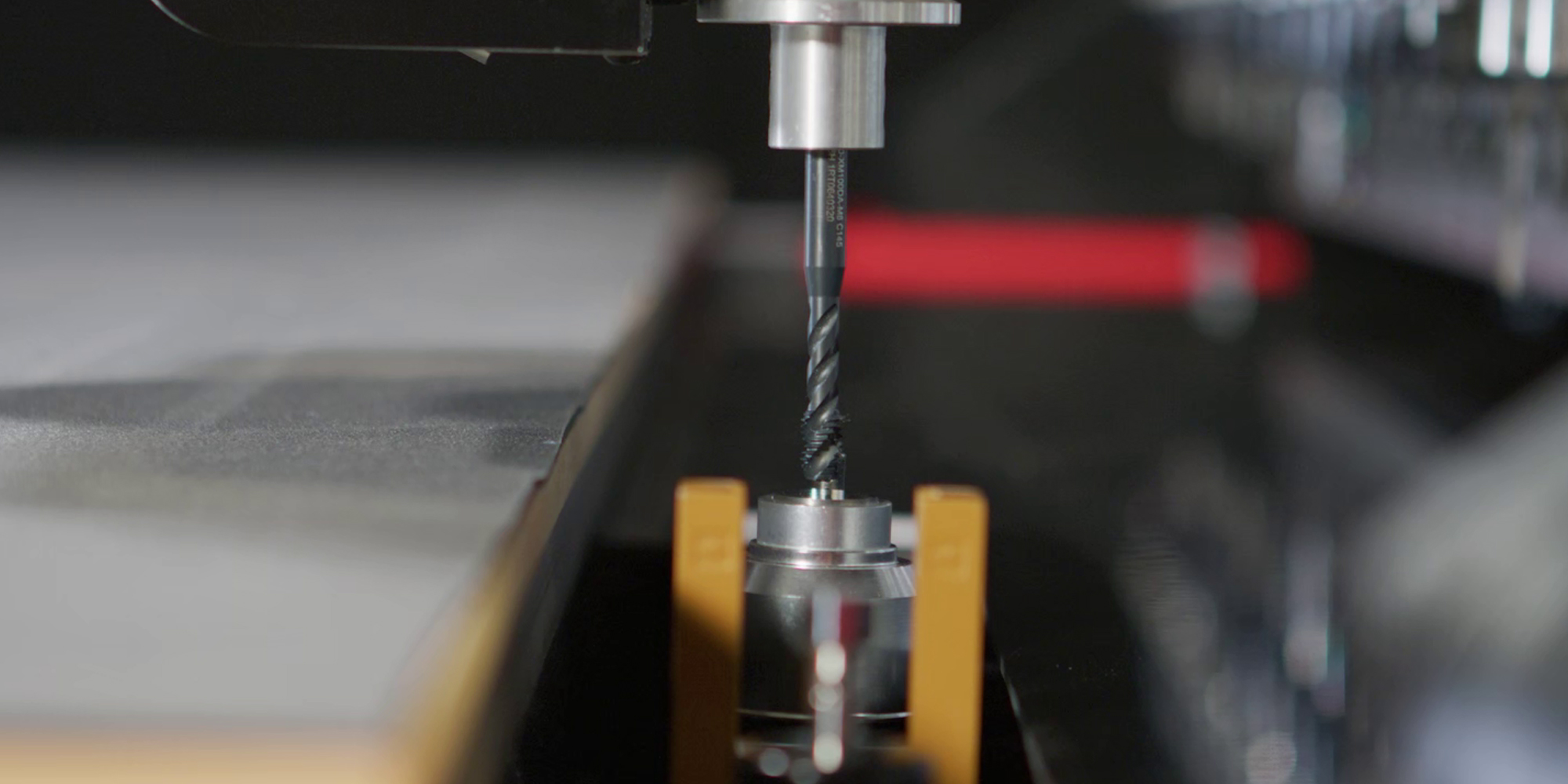
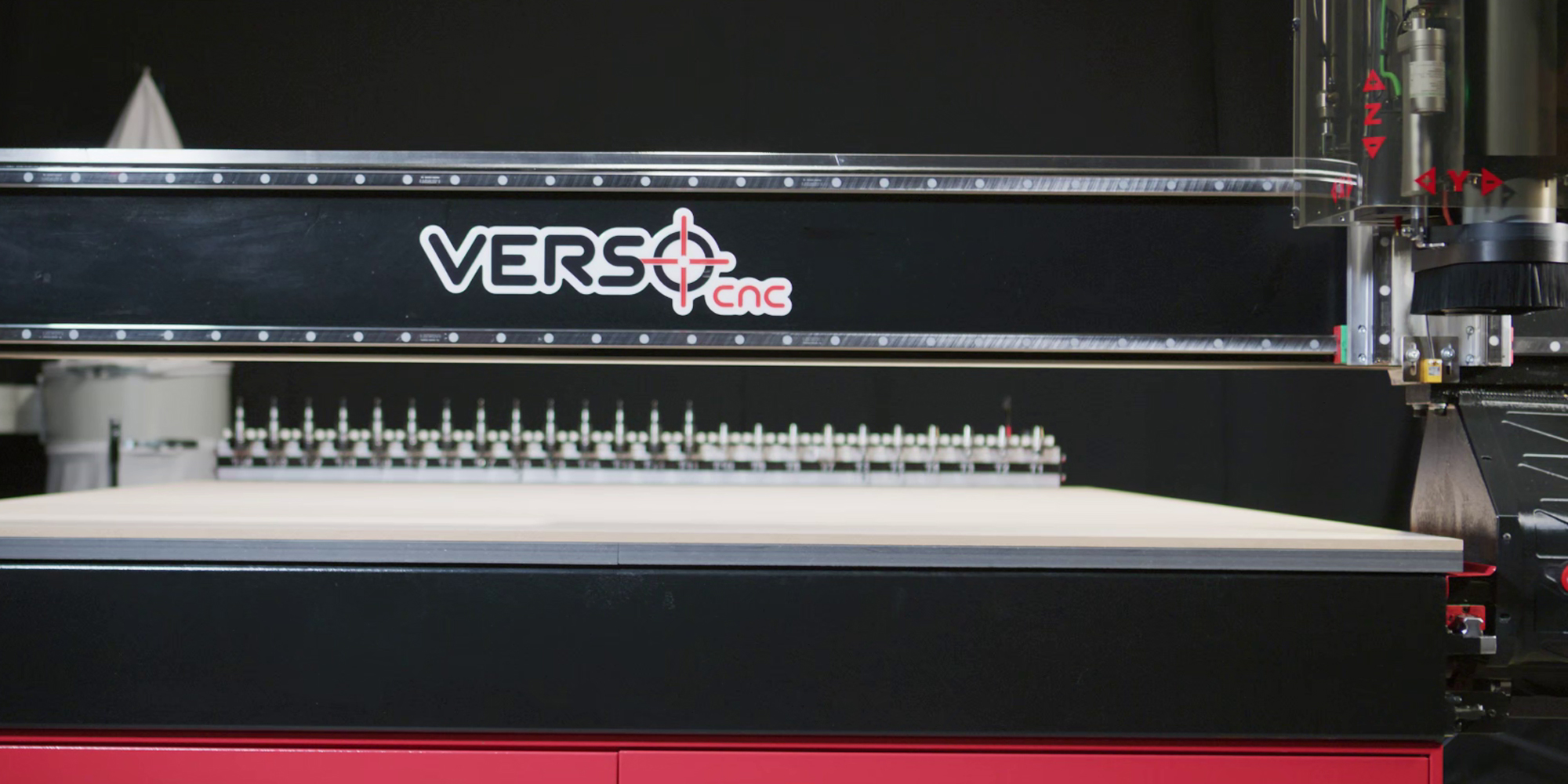
Sensing of table and flatness
The table of a large digital cutting machine is never perfect in the long term, that's a fact. Flatness defects can represent "slopes" of 0.05 to 0.07%. It seems quite little, but on a 3-metre table, the resulting depth inaccuracies often exceed a millimetre! The martyr can also present large flatness defects.
The table sensor fitted to the VSR makes it possible to periodically record its geometry in order to take it into account during cutting work.
N.B.: Thanks to this function, the VSR is one of the few milling machines capable of producing "hinges" on a 1.2 mm Hylite® plate on a daily basis (0.35 mm engraving on the front & back).
UTM, a multitude of features
We have created an extremely versatile module, capable of carrying very different tools. To take full advantage of it, we designed it so that it can use the ISO30 automatic tool changer present on our digital cutting tables.
Thanks to its powerful and downscaled shaft motor, it perfectly makes tangential cuts (blades, V-cutters and scoring wheels), but also taps. During these tasks, the UTM turns on itself, but remains locked on its vertical axis for perfect accuracy.
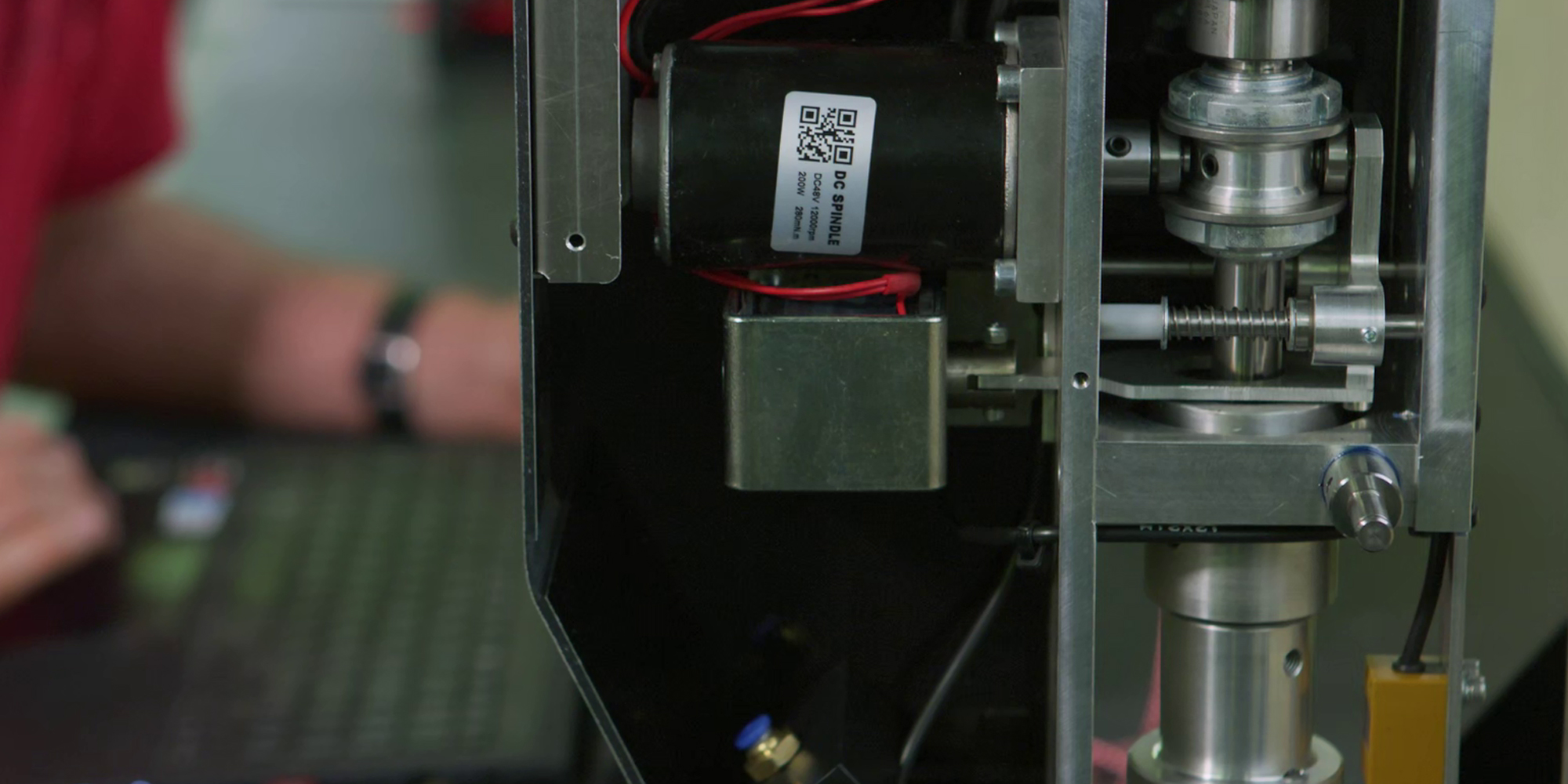
When it loads an oscillating type blade, the UTM releases its vertical axis and oscillates on its own.
The available tool holders:
- Tangential blade
- Oscillating blade
- V-cut blade (30, 45 or 60°)
- Scoring wheel
- Tap holder (choice of diam.)
By default, our "blade" tool holders are intended for round shank blades with a diameter of 6 mm, but we can make custom tool holders.
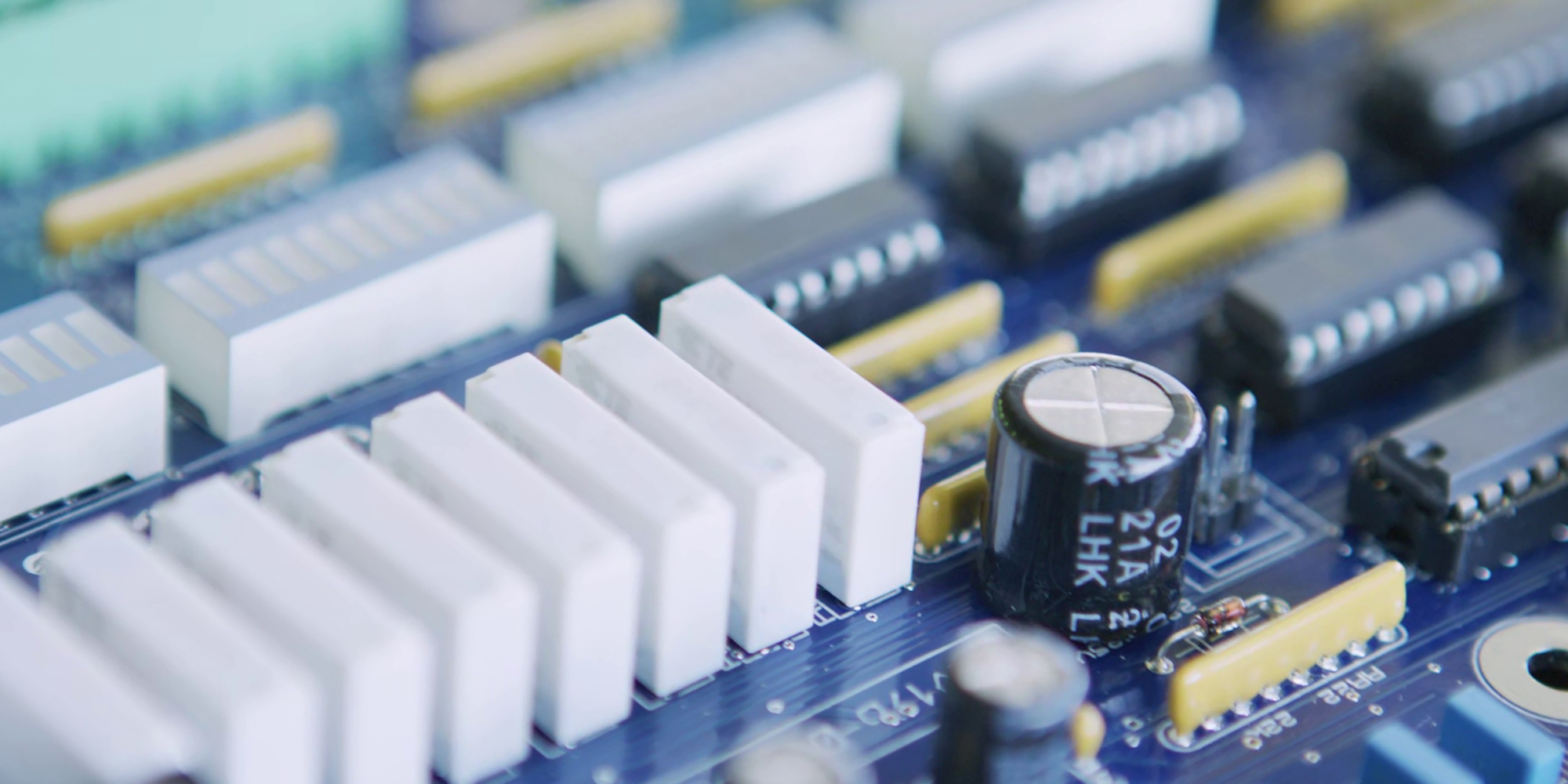
Control board
Like the CFAO VERSO CAM software, the control board is developed and manufactured by VERSO. It is fully dedicated to the functions and accessories present on the VS.
The powerful µc ARM Cortex + VERSO SPEEDDM firmware allows the VS to work at high speed with very fine resolutions.
Motorised suction brush
Far from being a gimmick, automatic positioning of the brush has many advantages. Indeed, it makes it possible to position the cutters and drills freely in the tool holders while ensuring good suction of the chips. The brush brushes against the material.
N.B.: For highly sensitive materials, a "Removal" function allows the brush to be positioned a few millimetres above the material during work.
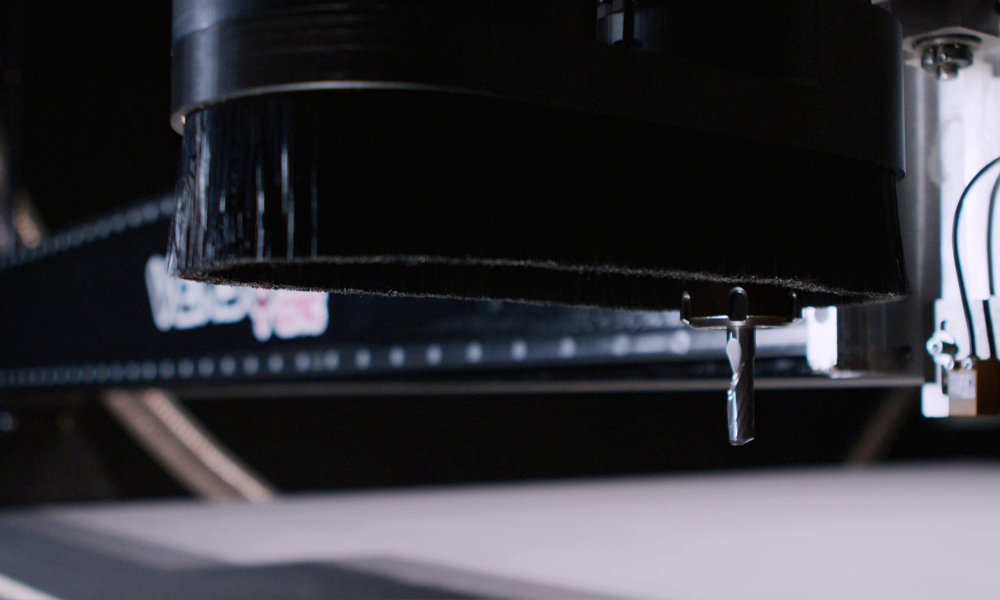
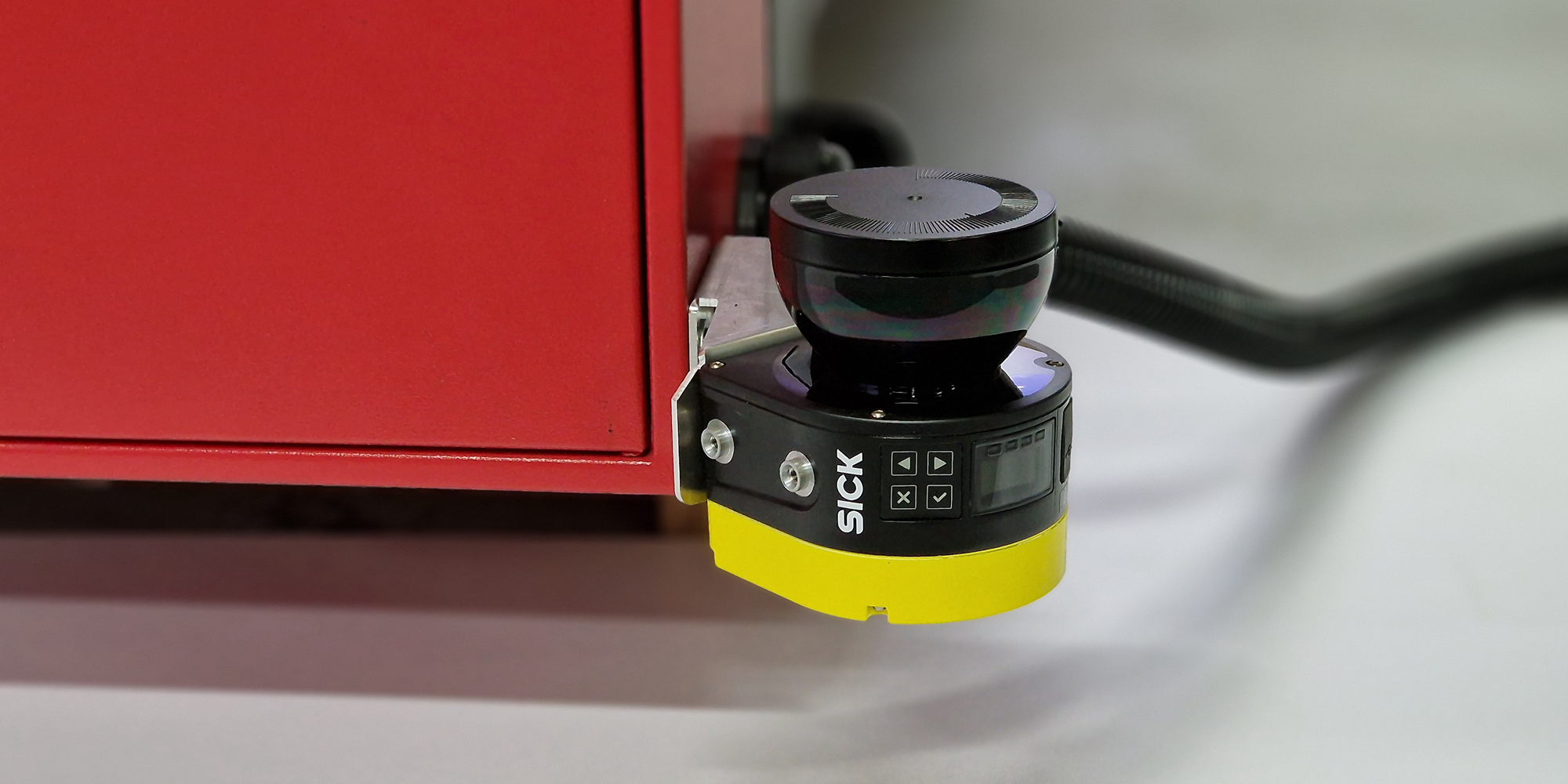
Sick® scanner (option)
Positioned at the corner of the machine on the console side, this LASER device detects any presence along the length and width of the machine.
If it is installed in the corner of a building, the perimeter is completely protected. When installing the machine along a wall, the device must be completed by a simple barrier at the bottom of the machine.
The detection zone is fully configurable through 275°, making it possible to exclude any obstacle (post, partition, etc.).
If the perimeter is crossed, the software immediately triggers a pause.
The work is resumed or abandoned by simply clicking on the window that appeared during the pause.
N.B.: If the scanner is inoperative or absent, or if an obstacle is within its detection perimeter upon the launch of the machine, the speed of movements is automatically limited to 30 m/min.
Accelerations are also reduced to 1 m.s².